Slurry seal machines are essential equipment for enhancing the lifespan and appearance of pavements. They are widely used in road maintenance and parking lot rejuvenation. This article will cover everything you need to know about slurry seal machines, from their components and types to their applications, benefits, and maintenance. Whether you’re a contractor, a municipality, or just someone interested in pavement preservation, this guide will provide valuable insights.
What is a Slurry Seal Machine?
A slurry seal machine is a specialized piece of equipment designed to apply a slurry seal—a mixture of asphalt emulsion, aggregate, and additives—onto pavement surfaces. The purpose of applying a slurry seal is to protect and rejuvenate the pavement, extending its useful life and enhancing its aesthetic appeal. Typically, slurry seal machines are used for roadways, parking lots, and other asphalt surfaces.
Components of a Slurry Seal Machine
1. Mixing Tank
The mixing tank is the core component where the materials are mixed to form a slurry. It is equipped with a high-capacity mixer that ensures a uniform blend of asphalt emulsion, aggregates, and other additives.
2. Pumping System
The pumping system is responsible for delivering the mixed slurry from the tank to the spray bar. These pumps are typically diaphragm or gear pumps that ensure a steady flow of the material.
3. Spray Bar
The spray bar is equipped with nozzles that evenly distribute the slurry onto the pavement. The adjustable nozzles allow for control over the application rate and width.
4. Control Panel
The control panel allows the operator to control various settings, including the mix ratio, application speed, and flow rates. Modern machines come equipped with electronic controls for increased precision.
5. Agitation System
An agitation system keeps the slurry mixed during the application process, preventing the materials from separating and ensuring consistent application.
Types of Slurry Seal Machines
1. Standard Slurry Seal Machines
Standard slurry seal machines are designed for general pavement applications. They can handle various asphalt emulsions and aggregates, making them suitable for most projects.
2. Micro-surfacing Machines
Micro-surfacing machines apply a thinner layer of slurry compared to standard sealers. They are often used for high-traffic areas that require quick drying times.
3. Patch and Repair Machines
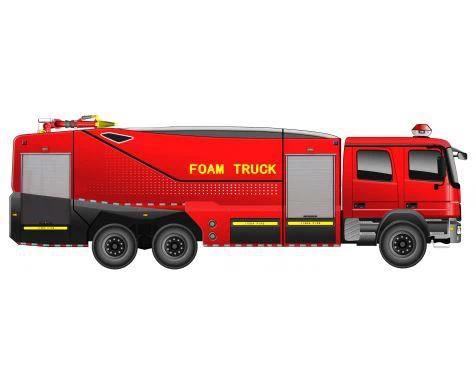
These machines are used for targeted repairs on pavement surfaces. They allow for precise application in small areas to address specific issues like cracks or surface damage.
Applications of Slurry Seal Machines
1. Road Maintenance
Slurry seal machines are commonly used by municipalities for maintaining city streets and highways. They help seal cracks, reduce surface deterioration, and improve skid resistance.
2. Parking Lot Rejuvenation
Commercial parking lots benefit greatly from slurry seals, which enhance their appearance while protecting them from the elements. Regular maintenance can save money by preventing costly repairs.
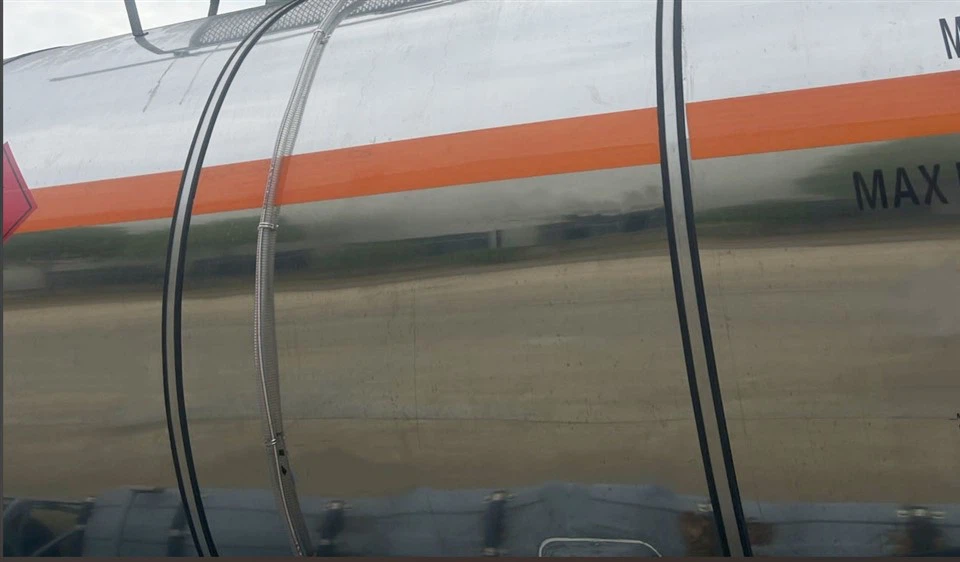
3. Sports Facilities
Many sports facilities utilize slurry seal machines to maintain asphalt courts and tracks. The sealing process improves the surface and provides better performance in athletic events.
4. Airport Runways
Slurry seal is also essential for airport runways, where friction and surface integrity are paramount for safety. Regular applications can significantly extend the life of runway surfaces.
Benefits of Using Slurry Seal Machines
1. Cost-Effectiveness
Using a slurry seal machine is a cost-effective solution for maintenance compared to complete resurfacing or reconstruction. It provides a protective layer that extends the life of existing pavements.
2. Enhanced Aesthetics
Slurry seals improve the visual appearance of pavements, creating a clean and uniform surface that can enhance property value.
3. Environmental Advantages
Slurry seals can incorporate recycled materials, reducing waste and environmental impact. Using asphalt emulsion also minimizes harmful emissions compared to traditional sealers.
4. Quick Application and Return to Service
Modern slurry seal machines offer fast application and quick drying, allowing traffic to return to the surface sooner, which is especially beneficial for busy areas.
How to Choose the Right Slurry Seal Machine
1. Project Size
Evaluate the scale of your project. Larger projects may require bigger machines with higher capacity, while smaller projects can be handled with compact machines.
2. Type of Application
Determine whether you need a standard slurry seal or micro-surfacing. Your choice of machine may depend on the specific applications you intend to conduct.
3. Budget Considerations
Calculate your budget for equipment purchase or rental. Ensure that the machine you choose offers a good balance of features and value for money.
4. Maintenance and Support
Consider the availability of spare parts and support services for maintenance. Opt for machines from manufacturers known for excellent customer service.
Practical Tips for Using a Slurry Seal Machine
1. Proper Preparation
Before using the slurry seal machine, ensure that the pavement surface is clean and free from debris. Any cracks should be filled, and potholes repaired.
2. Mix Ratio Optimization
Adjust the mix ratio according to the manufacturer’s specifications. Proper ratios ensure optimal performance and longevity of the slurry seal.
3. Monitor Weather Conditions
Choose to apply slurry seals in favorable weather conditions. Avoid applications during rain or extreme temperatures, as these can affect adhesion and curing.
4. Regular Maintenance of Equipment
Regularly service your slurry seal machine according to the manufacturer’s guidelines. This will ensure that the machine operates efficiently and has a longer lifespan.
Common Challenges When Using Slurry Seal Machines
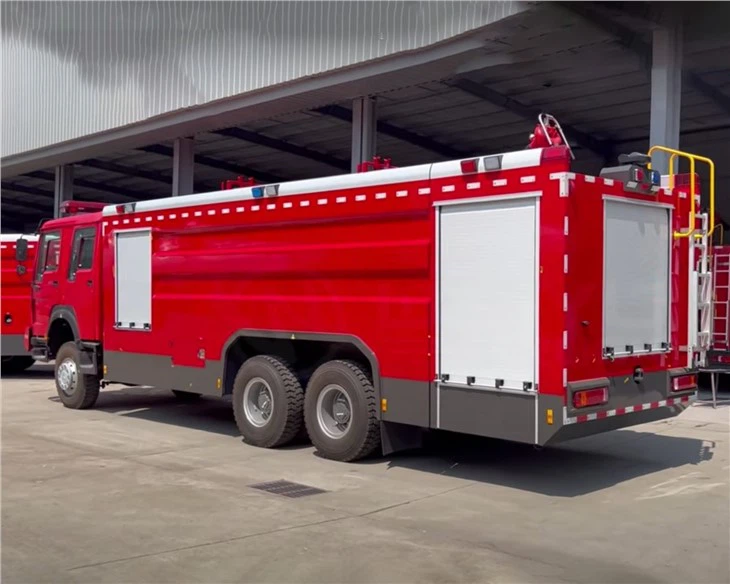
1. Uneven Surface Application
Uneven pavement can lead to an inconsistent slurry application. Always ensure surfaces are prepped and leveled before starting.
2. Material Separation
If the presence of aggregates in the slurry starts to separate, it can negatively impact the application. Ensure proper mixing and agitation during use.
3. Weather Interruptions
Weather can cause drying issues or affect adhesion. Plan your work schedule with the weather forecast in mind to avoid complications.
4. Operator Experience
Inexperienced operators may struggle with machine handling and application techniques. Adequate training is crucial for optimal results.
FAQs about Slurry Seal Machines
1. What is the difference between a slurry seal and micro-surfacing?
Slurry seal is typically used for preventive maintenance on lower traffic areas, while micro-surfacing is a thicker mix often applied in high-traffic environments for more durability.
2. How long does a slurry seal last?
With proper application and maintenance, a slurry seal can last anywhere from 5 to 10 years, depending on traffic conditions and weather factors.
3. Can I apply a slurry seal myself?
While it is possible to do it yourself, professional application is recommended to ensure quality results and avoid common pitfalls.
4. What materials are used in a slurry seal?
A typical slurry seal consists of asphalt emulsion, mineral aggregate, water, and sometimes additives like polymers for enhanced performance.
5. How do I maintain a slurry seal surface?
Regular cleaning, sealing of new cracks, and periodic reapplication when necessary are essential for maintaining a slurry seal surface.
6. What safety precautions should I take when using a slurry seal machine?
Always wear appropriate personal protective equipment (PPE), ensure proper ventilation if working indoors, and be aware of the machinery surroundings to prevent accidents.